Digital printing and flexographic printing are two distinct printing technologies that have revolutionized the printing industry. While their underlying processes and capabilities differ, they complement each other remarkably well, offering brands a powerful combination for various printing needs.
DIGITAL PRINTING
Digital printing is a modern method that directly transfers digital-based images, text, and graphics for a wide range of packaging types, including labels, flexible packaging, and shrink sleeves. Unlike traditional printing methods, digital printing does not require printing plates or cylinders, making it highly versatile and cost-effective for shorter print runs and personalized printing. Some of the advantages of digital printing include:
– Variable data printing: Digital printing allows for easy customization and personalization of each printed piece.
– Short print runs: Digital printing is ideal for small to medium print quantities, eliminating the need for costly plate setups.
– Quick turnaround times: Digital printing eliminates the need for plate-making and other prepress processes, enabling faster job completion.
– Wide range of substrates: Digital printing is used on various materials.
FLEXOGRAPHIC PRINTING
Flexographic printing, or flexo printing, is a high-speed, high-quality printing process widely used for packaging, labels, and other applications requiring large print runs. It utilizes flexible relief plates made of rubber or photopolymer materials to transfer ink onto a wide range of substrates, including paper, plastic, and metallic films. Flexographic printing offers several advantages:
– High-volume printing: Flexographic printing is highly efficient for large print runs, making it cost-effective for high-volume applications.
– Versatile substrate compatibility: Flexographic printing is utilized on various substrates, including label stock, flexible films, and non-porous materials.
– High print quality: Modern flexographic printing techniques can achieve high-quality prints with precise color reproduction and sharp image details.
– Environmentally friendly: Flexographic printing uses water-based or UV-curable inks, generally more environmentally friendly than solvent-based inks.
COMPLEMENTARY NATURE
While digital printing and flexographic printing have distinct strengths and limitations, they can work together seamlessly to provide businesses with a comprehensive printing solution. By combining these two technologies, Custom Label can leverage the benefits of both methods, optimizing their printing processes for different job requirements and print volumes.
The Rise of Digital Printing and its Impact
The printing industry has undergone a significant transformation with the advent of digital printing technology. Several factors have driven the rapid growth and adoption of digital printing methods, revolutionizing how businesses approach their printing needs.
One of the primary drivers behind the rise of digital printing is its ability to handle short-run and variable data printing efficiently. Due to the setup costs involved, traditional printing methods, such as offset and flexographic, are more cost-effective for large print runs. However, digital printing eliminates the need for costly plate-making and setup processes, making it an attractive option for smaller print runs and personalized or customized printing jobs.
The benefits of digital printing extend beyond cost-effectiveness for smaller print runs. It also offers unparalleled flexibility and responsiveness, allowing businesses to adapt to changing market demands and customer preferences quickly. With digital printing, companies can easily modify designs, text, or graphics on the fly, enabling them to produce highly targeted and personalized marketing materials, packaging, or other printed materials.
Moreover, digital printing has revolutionized how businesses approach variable data printing (VDP). VDP involves the creation of unique versions of a printed piece, each tailored to specific individuals or segments. This capability has proven invaluable in direct marketing campaigns, personalized catalogs, and targeted promotional materials, resulting in higher engagement and response rates.
The cost-effectiveness of digital printing for smaller print runs has also opened up new opportunities for businesses of all sizes. Small and medium-sized enterprises can now access high-quality printing services without the significant upfront costs of traditional printing methods. This democratization of printing has leveled the playing field, allowing small companies to compete with larger corporations in terms of marketing and branding efforts.
Overall, the rise of digital printing has disrupted the traditional printing landscape, offering businesses greater flexibility, cost-effectiveness, and the ability to produce highly targeted and personalized printed materials. As digital printing technology continues to evolve, its impact on the industry will continue to grow, driving innovation and reshaping the way businesses approach their printing needs.
Flexographic Printing: A Powerhouse for High-Volume Runs
Flexographic printing has long been a favored choice for high-volume printing applications, offering unparalleled efficiency and cost-effectiveness. This rotary printing technique utilizes flexible relief plates wrapped around rotating cylinders, allowing continuous printing on a wide range of substrates, including paper, plastic, metallic films, and even corrugated materials.
One of the key advantages of flexographic printing is its ability to handle large print runs with remarkable speed and consistency. The seamless web-fed process ensures a continuous flow of material, enabling rapid production rates that can reach up to 1,500 feet per minute. This makes flexographic printing an ideal solution for applications that require high volumes, such as packaging materials, labels, and flexible packaging.
Moreover, flexographic printing excels in its versatility, accommodating a diverse array of substrates with varying thicknesses and surface properties. The flexible plates can conform to the substrate’s contours, from labels to films, ensuring precise and consistent ink transfer. This adaptability allows for printing on materials that may be challenging for other printing methods, expanding the range of applications and products that can benefit from flexographic printing.
Another significant advantage of flexographic printing is its cost-effectiveness for high-volume runs. Once the initial setup is complete, the printing process becomes highly efficient, minimizing material waste and reducing overall production costs. This makes flexographic printing an economically viable choice for large-scale manufacturing operations, where cost savings can significantly impact profitability.
In addition to its speed and cost-effectiveness, flexographic printing has made remarkable strides in print quality. Modern flexographic presses, coupled with advanced plate-making technologies and high-definition printing plates, can produce vibrant, sharp, and detailed images that rival the quality of other printing methods. This continuous improvement in print quality has further solidified flexographic printing’s position as a powerful solution for various applications, from consumer packaged goods to promotional materials.
Complementary Strengths: Combining Digital and Flexographic Printing
The true power of digital and flexographic printing lies in their complementary strengths, allowing Custom Label to leverage the advantages of both technologies for optimized printing solutions. By seamlessly integrating these two printing methods, companies can unlock possibilities, delivering high-quality, cost-effective, and versatile printing outcomes.
Digital printing produces short to medium-print runs with exceptional variability and personalization capabilities. Its ability to print-on-demand and eliminate the need for plates or cylinders makes it an ideal choice for applications that require frequent design changes, versioning, or variable data printing. Additionally, digital printing offers faster turnaround times and lower setup costs, making it a cost-effective solution for smaller print runs.
On the other hand, flexographic printing shines in high-volume, long-run applications, offering exceptional print quality and consistency. Its ability to print on various substrates, including flexible packaging materials, labels, and corrugated boards, makes it a versatile choice for various industries. Flexographic printing also provides excellent color reproduction, ensuring vibrant and accurate colors across large print runs.
By combining these two printing methods, businesses can leverage the strengths of each technology to create a robust printing solution. Digital printing can be used for prototyping, short runs, or personalized printing, while flexographic printing can handle high-volume production runs. This approach allows for efficient and cost-effective printing, minimizing waste and maximizing productivity.
The combination of digital and flexographic printing offers a versatile solution that caters to a wide range of industries and applications. This powerful printing duo enables businesses to leverage both technologies’ strengths, resulting in increased efficiency, cost-effectiveness, and customization capabilities.
The packaging sector has embraced the synergy between digital and flexographic printing, particularly in labels, flexible packaging, and folding cartons. Digital printing allows for short-run, customized packaging solutions, while flexographic printing excels at high-volume runs with consistent quality. This combination enables manufacturers to produce personalized packaging for targeted marketing campaigns, limited editions, or localized products while also meeting the demands of mass production.
DIGITAL PRINTING
Digital printing is a modern method that directly transfers digital-based images, text, and graphics for a wide range of packaging types, including labels, flexible packaging, and shrink sleeves. Unlike traditional printing methods, digital printing does not require printing plates or cylinders, making it highly versatile and cost-effective for shorter print runs and personalized printing. Some of the advantages of digital printing include:
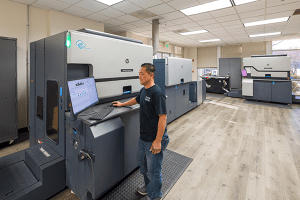
– Short print runs: Digital printing is ideal for small to medium print quantities, eliminating the need for costly plate setups.
– Quick turnaround times: Digital printing eliminates the need for plate-making and other prepress processes, enabling faster job completion.
– Wide range of substrates: Digital printing is used on various materials.
FLEXOGRAPHIC PRINTING
Flexographic printing, or flexo printing, is a high-speed, high-quality printing process widely used for packaging, labels, and other applications requiring large print runs. It utilizes flexible relief plates made of rubber or photopolymer materials to transfer ink onto a wide range of substrates, including paper, plastic, and metallic films. Flexographic printing offers several advantages:
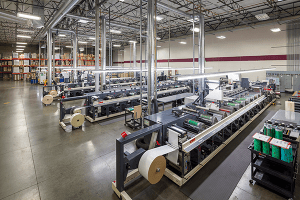
– High-volume printing: Flexographic printing is highly efficient for large print runs, making it cost-effective for high-volume applications.
– Versatile substrate compatibility: Flexographic printing is utilized on various substrates, including label stock, flexible films, and non-porous materials.
– High print quality: Modern flexographic printing techniques can achieve high-quality prints with precise color reproduction and sharp image details.
– Environmentally friendly: Flexographic printing uses water-based or UV-curable inks, generally more environmentally friendly than solvent-based inks.
COMPLEMENTARY NATURE
While digital printing and flexographic printing have distinct strengths and limitations, they can work together seamlessly to provide businesses with a comprehensive printing solution. By combining these two technologies, Custom Label can leverage the benefits of both methods, optimizing their printing processes for different job requirements and print volumes.
The Rise of Digital Printing and its Impact
The printing industry has undergone a significant transformation with the advent of digital printing technology. Several factors have driven the rapid growth and adoption of digital printing methods, revolutionizing how businesses approach their printing needs.
One of the primary drivers behind the rise of digital printing is its ability to handle short-run and variable data printing efficiently. Due to the setup costs involved, traditional printing methods, such as offset and flexographic, are more cost-effective for large print runs. However, digital printing eliminates the need for costly plate-making and setup processes, making it an attractive option for smaller print runs and personalized or customized printing jobs.
The benefits of digital printing extend beyond cost-effectiveness for smaller print runs. It also offers unparalleled flexibility and responsiveness, allowing businesses to adapt to changing market demands and customer preferences quickly. With digital printing, companies can easily modify designs, text, or graphics on the fly, enabling them to produce highly targeted and personalized marketing materials, packaging, or other printed materials.
Moreover, digital printing has revolutionized how businesses approach variable data printing (VDP). VDP involves the creation of unique versions of a printed piece, each tailored to specific individuals or segments. This capability has proven invaluable in direct marketing campaigns, personalized catalogs, and targeted promotional materials, resulting in higher engagement and response rates.
The cost-effectiveness of digital printing for smaller print runs has also opened up new opportunities for businesses of all sizes. Small and medium-sized enterprises can now access high-quality printing services without the significant upfront costs of traditional printing methods. This democratization of printing has leveled the playing field, allowing small companies to compete with larger corporations in terms of marketing and branding efforts.
Overall, the rise of digital printing has disrupted the traditional printing landscape, offering businesses greater flexibility, cost-effectiveness, and the ability to produce highly targeted and personalized printed materials. As digital printing technology continues to evolve, its impact on the industry will continue to grow, driving innovation and reshaping the way businesses approach their printing needs.
Flexographic Printing: A Powerhouse for High-Volume Runs
Flexographic printing has long been a favored choice for high-volume printing applications, offering unparalleled efficiency and cost-effectiveness. This rotary printing technique utilizes flexible relief plates wrapped around rotating cylinders, allowing continuous printing on a wide range of substrates, including paper, plastic, metallic films, and even corrugated materials.
One of the key advantages of flexographic printing is its ability to handle large print runs with remarkable speed and consistency. The seamless web-fed process ensures a continuous flow of material, enabling rapid production rates that can reach up to 1,500 feet per minute. This makes flexographic printing an ideal solution for applications that require high volumes, such as packaging materials, labels, and flexible packaging.
Moreover, flexographic printing excels in its versatility, accommodating a diverse array of substrates with varying thicknesses and surface properties. The flexible plates can conform to the substrate’s contours, from labels to films, ensuring precise and consistent ink transfer. This adaptability allows for printing on materials that may be challenging for other printing methods, expanding the range of applications and products that can benefit from flexographic printing.
Another significant advantage of flexographic printing is its cost-effectiveness for high-volume runs. Once the initial setup is complete, the printing process becomes highly efficient, minimizing material waste and reducing overall production costs. This makes flexographic printing an economically viable choice for large-scale manufacturing operations, where cost savings can significantly impact profitability.
In addition to its speed and cost-effectiveness, flexographic printing has made remarkable strides in print quality. Modern flexographic presses, coupled with advanced plate-making technologies and high-definition printing plates, can produce vibrant, sharp, and detailed images that rival the quality of other printing methods. This continuous improvement in print quality has further solidified flexographic printing’s position as a powerful solution for various applications, from consumer packaged goods to promotional materials.
Complementary Strengths: Combining Digital and Flexographic Printing
The true power of digital and flexographic printing lies in their complementary strengths, allowing Custom Label to leverage the advantages of both technologies for optimized printing solutions. By seamlessly integrating these two printing methods, companies can unlock possibilities, delivering high-quality, cost-effective, and versatile printing outcomes.
Digital printing produces short to medium-print runs with exceptional variability and personalization capabilities. Its ability to print-on-demand and eliminate the need for plates or cylinders makes it an ideal choice for applications that require frequent design changes, versioning, or variable data printing. Additionally, digital printing offers faster turnaround times and lower setup costs, making it a cost-effective solution for smaller print runs.
On the other hand, flexographic printing shines in high-volume, long-run applications, offering exceptional print quality and consistency. Its ability to print on various substrates, including flexible packaging materials, labels, and corrugated boards, makes it a versatile choice for various industries. Flexographic printing also provides excellent color reproduction, ensuring vibrant and accurate colors across large print runs.
By combining these two printing methods, businesses can leverage the strengths of each technology to create a robust printing solution. Digital printing can be used for prototyping, short runs, or personalized printing, while flexographic printing can handle high-volume production runs. This approach allows for efficient and cost-effective printing, minimizing waste and maximizing productivity.
The combination of digital and flexographic printing offers a versatile solution that caters to a wide range of industries and applications. This powerful printing duo enables businesses to leverage both technologies’ strengths, resulting in increased efficiency, cost-effectiveness, and customization capabilities.
The packaging sector has embraced the synergy between digital and flexographic printing, particularly in labels, flexible packaging, and folding cartons. Digital printing allows for short-run, customized packaging solutions, while flexographic printing excels at high-volume runs with consistent quality. This combination enables manufacturers to produce personalized packaging for targeted marketing campaigns, limited editions, or localized products while also meeting the demands of mass production.